- หน้าแรก
- REBAR _S (ACI)
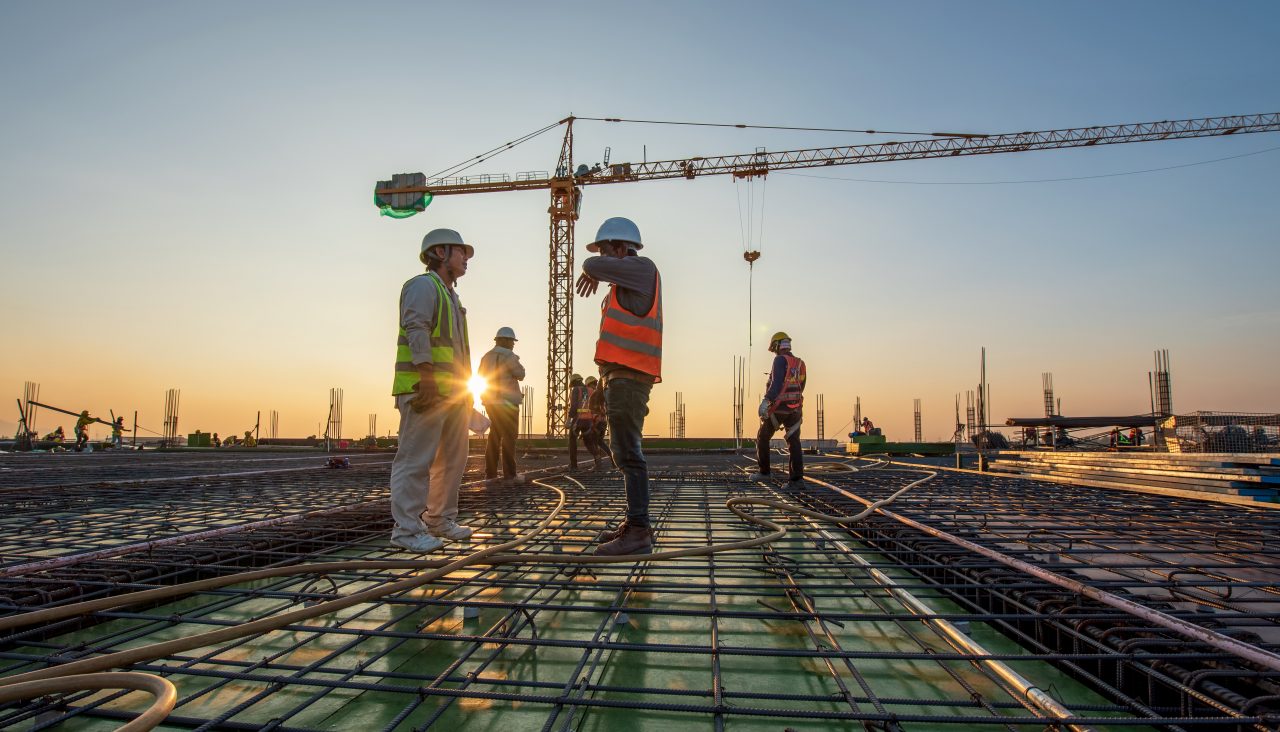
Safety demands rebar connection design
Qualified Products | Compliant Design | Safe Installation
At Hilti, we understand the critical nature of structural concrete connections in ensuring the integrity and robustness of your structure throughout its lifecycle. Whether a new build or a retrofit, we offer end-to-end post-installed rebar solutions. Our mortars are qualified as per ICC Evaluation Service Reports (ESRs) for use with structural concrete design standards for typical connections such as end anchorages, splices, overlays, and beyond. With our easy-to-use design software and safe and reliable installation tools, reduce the risk of errors and speed up your construction.
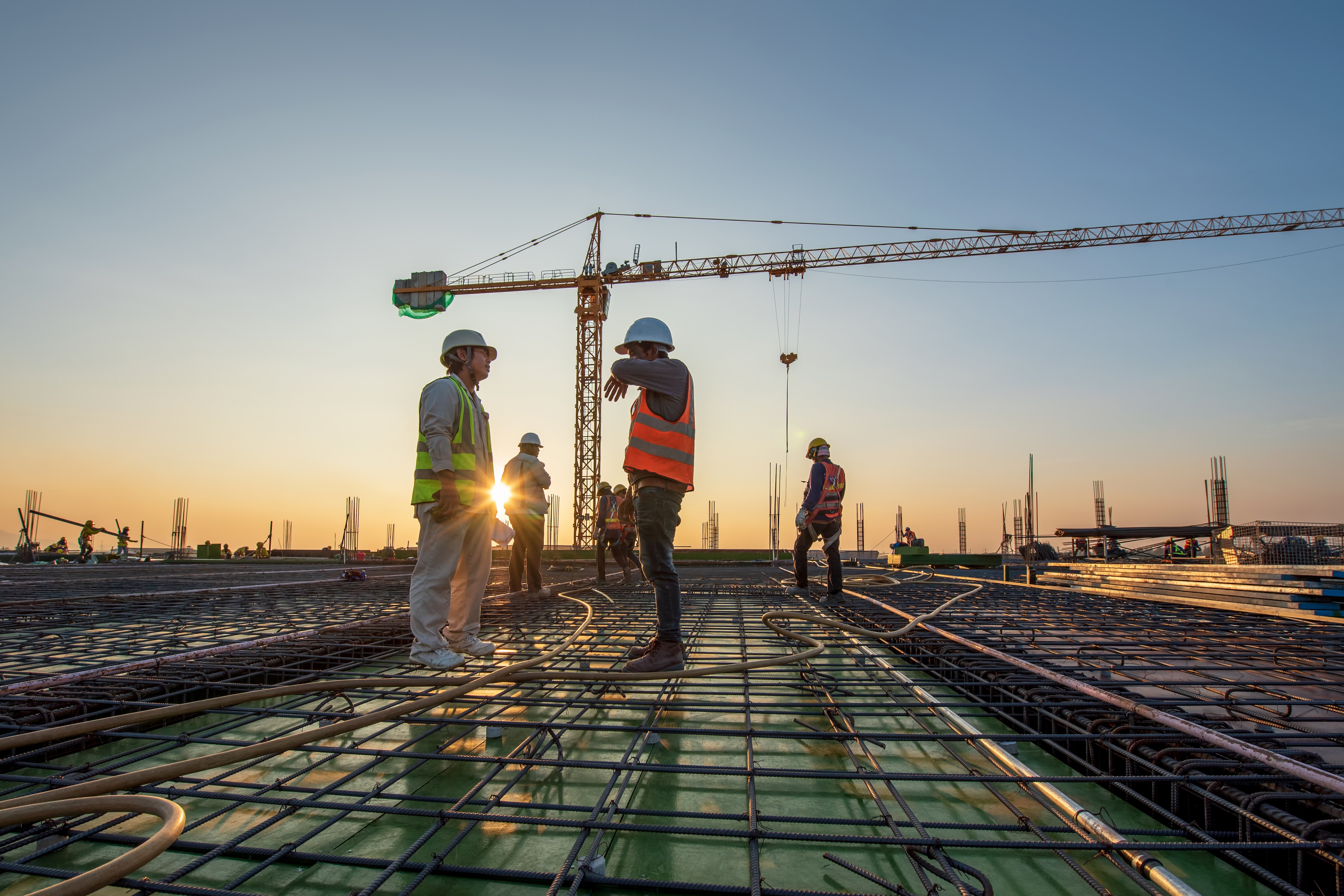
Upcoming Webinars
-
Please come back again to look out for any upcoming webinars
Please visit again thank you
POST-INSTALLED REBAR & TYPE OF APPLICATION
Post-installed reinforcing bars are typically used to develop a monolithic connection between new and existing concrete elements or structures. Post-installed reinforcing bars are used in both retrofit work and in new construction and are suitable for a wide range of applications. Let’s look at some of the common rebar applications below.
IMPORTANCE OF DESIGN
To ensure that the post-installed reinforcing bar behaves as a cast-in bar, it is important that the type, size, spacing and quantity and anchorage be established for the connection. This is typically based on either direct calculation of section forces, or a requirement to match existing reinforcement. Hence, design of rebar connections are important to achieve desired results.
The rebar applications mentioned below can be clustered into 3 categories and have different design requirements.
End Anchorages
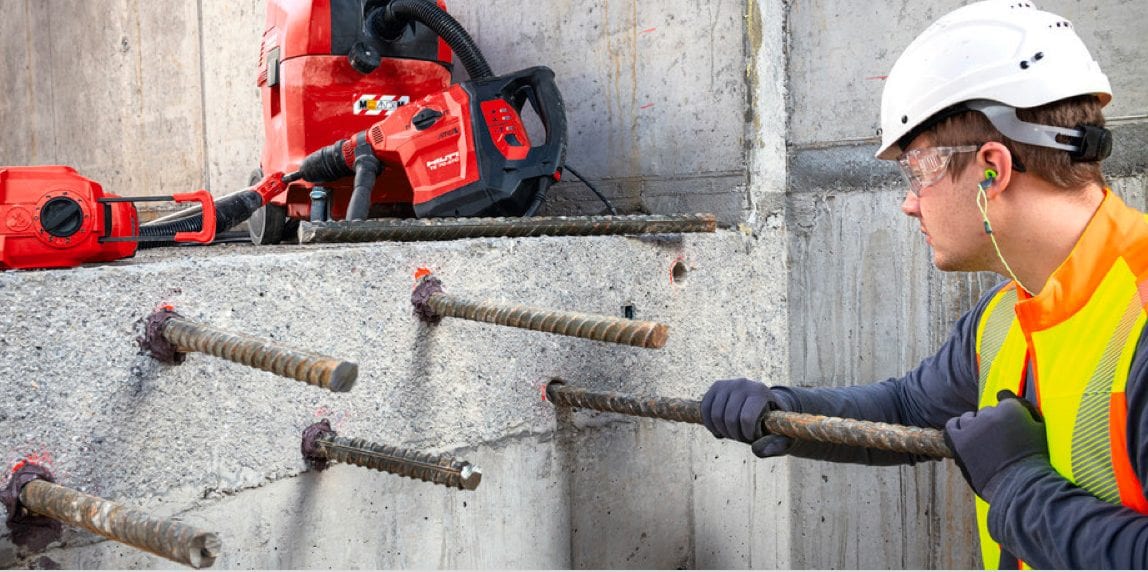
End anchorages involve connecting new concrete elements perpendicular to existing ones. Examples include beam-to-column, slab-to-wall, column-to-foundations, and so on.
Splices
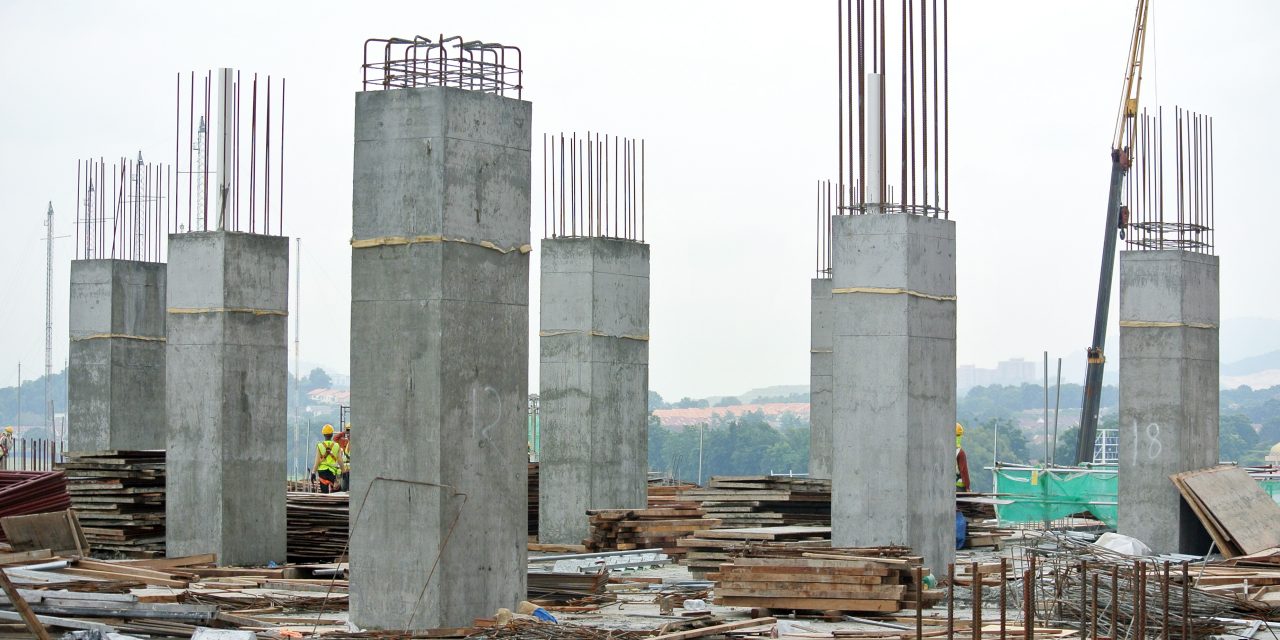
Lap splices involve extending existing concrete elements parallel to existing ones. The new bars are not in contact with existing ones. Examples include beam extension, column extension, slab extension etc.
Qualification Per ICC AC308
End Anchorage
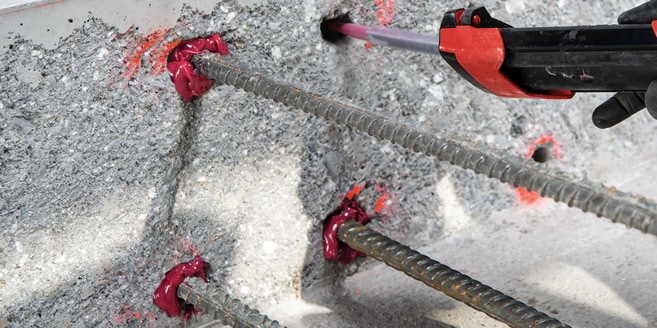
Assessment with ICC AC308 establishes equivalence of the adhesive mortar systems to cast-in-place rebars in terms of load-displacement behavior, bond-splitting resistance, and robustness under different installation, environmental, and loading conditions.
Splices
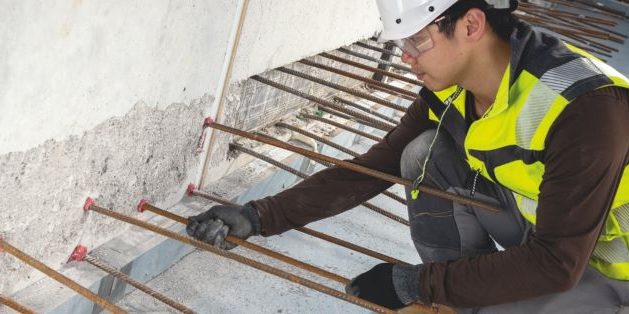
Assessment with ICC AC308 establishes equivalence of the adhesive mortar systems to cast-in-place rebars in terms of load-displacement behavior, bond-splitting resistance, and robustness under different installation, environmental, and loading conditions.
Concrete Overlay
ICC Acceptance Criteria AC308 assesses the performance and behaviour of post-installed rebar connecting to concrete layers subject to different installation, environmental, and loading conditions. The shear dowel must ensure monolithic behaviour and the corresponding ICC-ESR provides data for use in design.
Design Criterias
End Anchorages
For end anchorages, once the design of the new section and required reinforcement is complete, calculation of the development length, ld, is required to safely transfer the stress in the bar to existing concrete member. This is undertaken with the same provisions for cast-in bars as in Chapter 25 of ACI 318-14 & -19.
Additional checks involve complying with requirements such as the project’s design or service life, and the minimum development length requirements of ACI 318.
Splices
For lap splices, once the design of the new section and required reinforcement is complete, calculation of the development length, ld, is required to safely transfer the stress in the bar to the bars in the existing concrete member. This is undertaken with the same provisions for cast-in bars as in Chapter 25 of ACI 318-14 & -19.
Additional checks involve complying with requirements such as the project’s design or service life, and the minimum development length requirements of ACI 318.
Concrete Overlay
Design follows the provisions of Chapters 22 and 25 of ACI 318-14 & -19 and is centered on calculating the resistance of the entire interface based on the contributions of friction and the full yield strength of the dowel action of the bar. Based on the modified shear-friction theory, increasing roughness results in increased friction that reduces the number of required bars crossing the interface.
The designer must specify the roughness class desired at site since this strongly influences the design. The roughness class may be determined by the “sand patch” or “mean depth” methods, or through optical profilometry.
Select the appropriate design approach
PROFIS Engineering Concrete to Concrete Module
Everything you need to design post-installed rebar applications
Add or extend concrete elements whether you're working with existing rebar or missing starter bars. Solve concrete structural joints and splices, and then verify the shear resistance at the interface between the old and new concrete.
Need to adapt the layout or geometry of your PIR design? PROFIS lets you easily customize the diameter, embedment depth and spacing parameters for existing concrete as well as post-installed.
Use PROFIS Engineering Concrete to Concrete ModuleRequest rebar design from Hilti
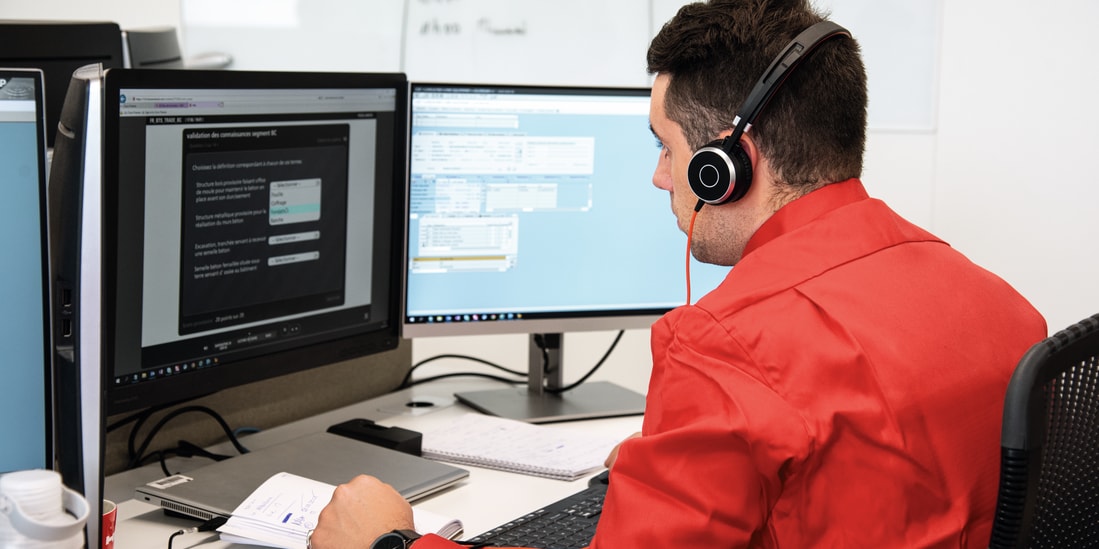
Hilti Rebar Design service to assist you in the design and calculation of your Rebar Applications with the most optimized solution for you.
Our service includes:
- Cover letter
- Checklist including summary of request and input details
- Detailed bill of material per application
- Complete software calculation report per application
- PROFIS Rebar design file per application
- Specification text
Design your connection for demanding conditions
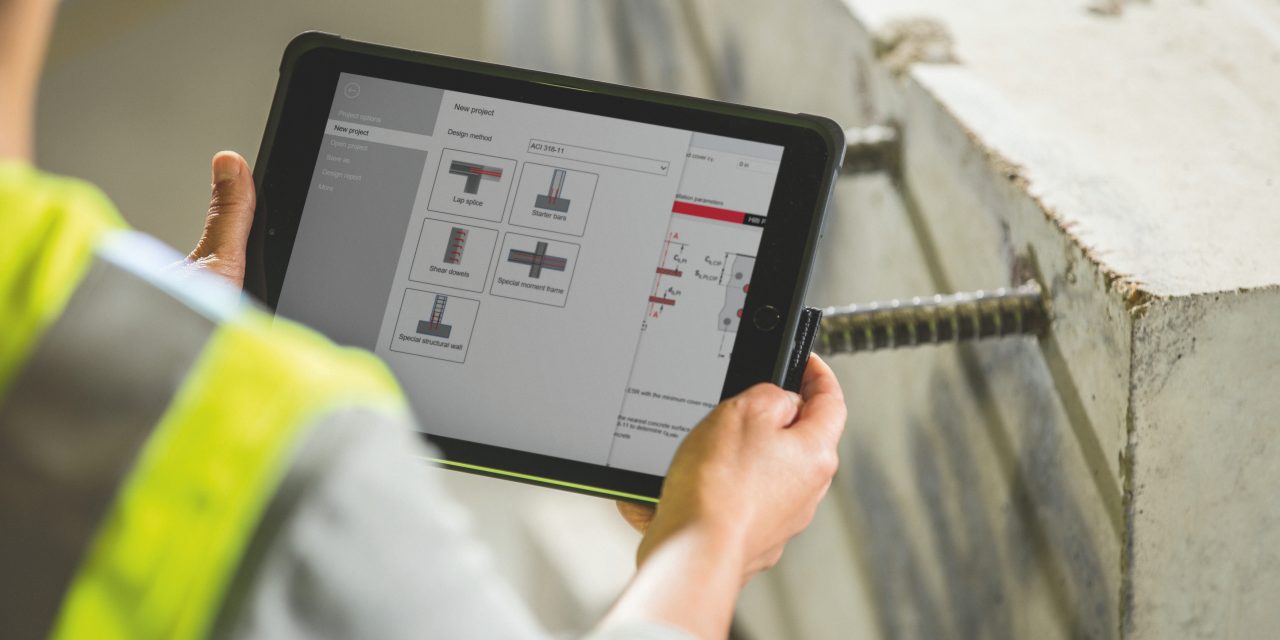
Static Design
This is the most common class of applications for post-installed rebars and includes the connection of new components to an existing structure. According to structural concrete building codes, the bond strength of cast-in bars is limited, even where depth of concrete cover is considerable. And so, in some areas, such as walls where anchorage depth is often limited, welded transverse reinforcement or hooks are used to compensate for the reduction in available anchorage length.
Download design code Download design guideline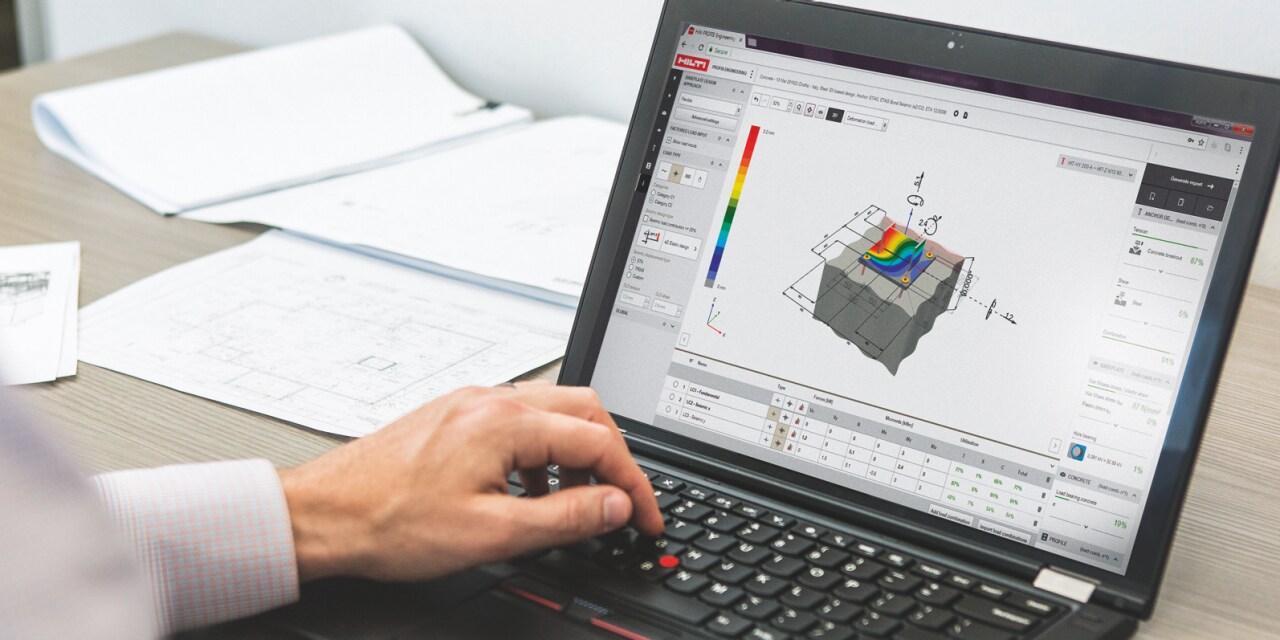
Seismic Design
An increasing population density, the concentration of valuable assets in urban centers and society’s dependence on a functioning infrastructure demand a better understanding of the risks posed by earthquakes. In several areas around the globe, these risks have been reduced through appropriate building codes and state of the art construction practices. The development of pre-qualification methods to evaluate building products for seismic conditions additionally contributes to safer buildings for generations to come.
Watch recorded webinar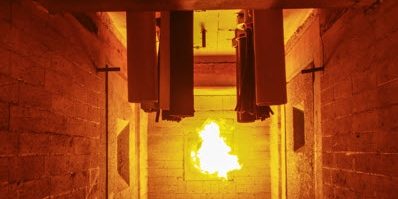
Fire Design
Organic adhesives are affected by high temperatures. For post-installed rebar connections that are part of a fire-resisting assembly (floor, roof, etc.), evaluating the fire resistance of the connection is key to ensure safety. Currently, AC308 does not have the provisions to qualify a mortar to elevated temperatures. However, designers may find the European equivalent (EAD 330087) relevant as it provides a time-dependent reduction in bond strength associated with typical geometries and time-temperature loading protocols for specific assessed mortars.
INSTALL POST-INSTALLED REBAR CORRECTLY
Proper installation is important to ensure that the post installed rebar behaves as designed. The following installation steps must be followed at the jobsite in the same order to ensure the safety of the rebar connection.
POSITION
Scanning
Scanning of the surface avoids cutting through existing reinforcement and drilling unnecessary holes.
Hitli PS 300 has an integrated display to provide rebar layout visuals in top view and sectional view for on-the-spot structural analysis.
Watch VideoDRILL
Drilling for rebar
Drill faster and safely with Hilti combi-hammers and extra-rugged Hilti hammer drill bits
Hilti TE 30 has Active Torque Control (ATC) stops the tool body from spinning uncontrolledly if the drill bit jams.
Watch VideoCLEAN
SafeSet
Inadequately cleaning holes during installation can reduce the performance of chemical anchor systems significantly.
Hilti SAFEST Technology eliminates this factor almost entirely by automatically cleaning the hole while drilling.
INJECT MORTAR
Inject chemical using Piston Plug
Injecting the right amount of chemical is important to ensure that the chemical sets around the rebar o bond with concrete.
With the help of our cordless adhesive anchor dispenser, the right amount of anchor is injected with a single push of a button. You achieve the accuracy you need, while using up to 30% less resin.
Watch VideoSET REBAR
Rebar setting
For easy installation, the rebar must be inserted slowly twisted into the drill hole until the embedment mark. Twisting the rebar, eliminates the air bubbles and ensures chemical is evenly spread around the bar.
Watch VideoJobsite References
NATHDWARA INDIA
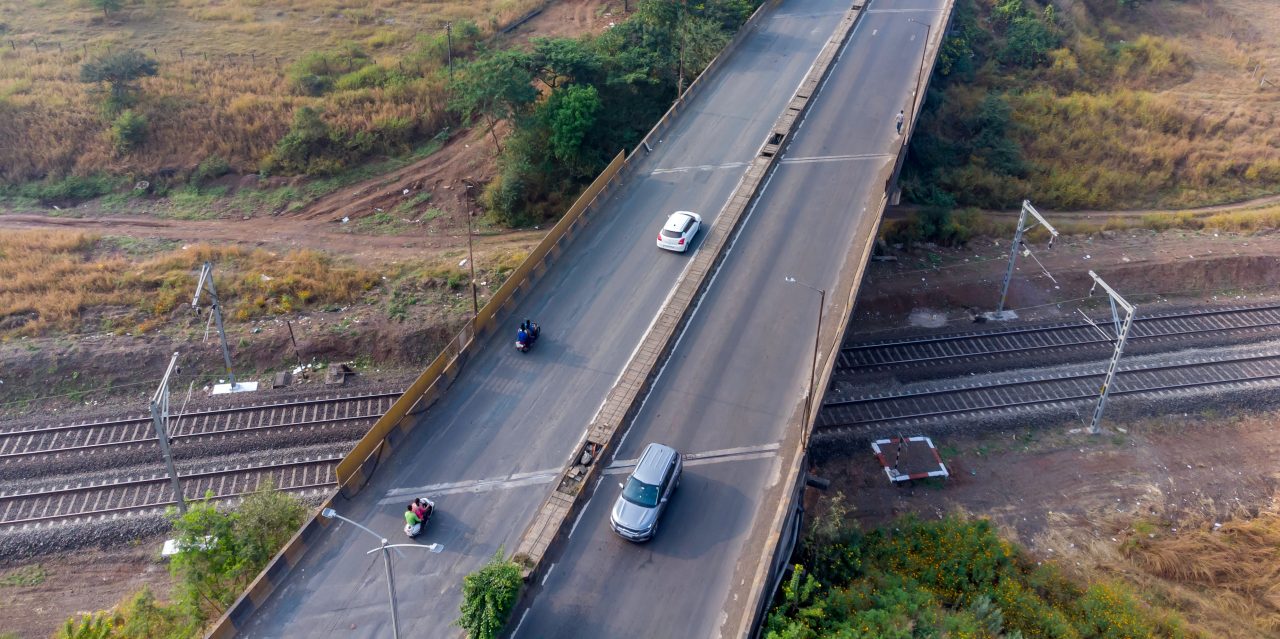
Protecting a major road bridge from earthquakes
The bridge at Nathdwara has a steep curve in it and needed seismic stoppers to stop the bridge sliding in an earthquake.
DELHI METRO
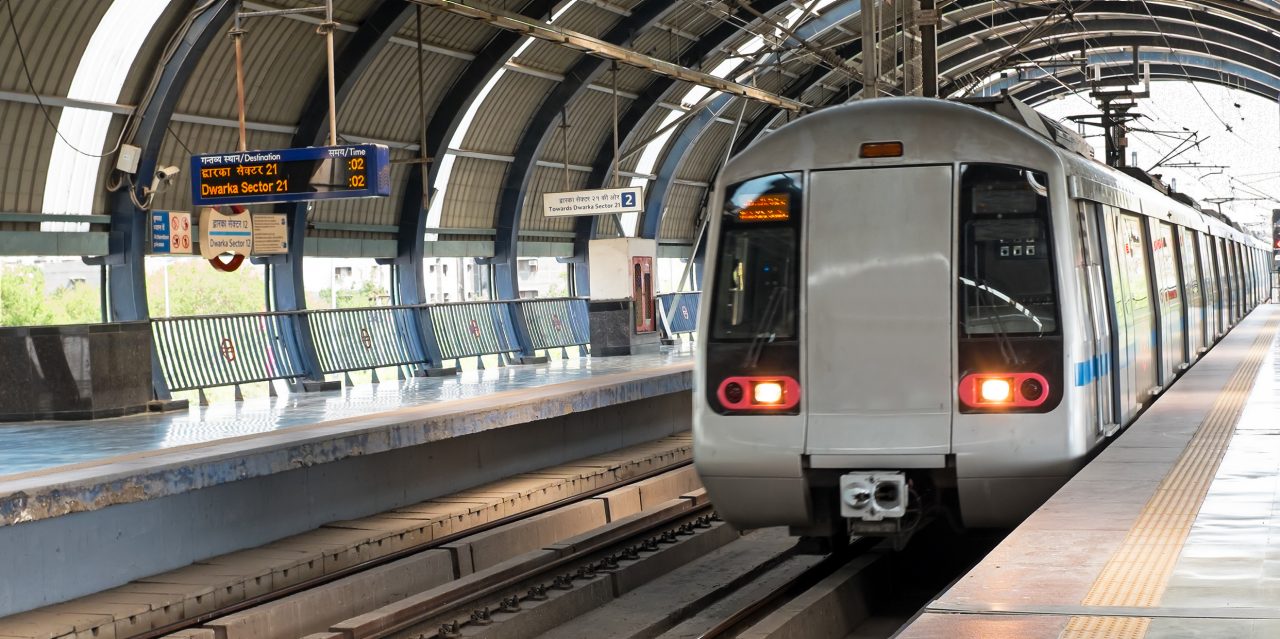
Using post-installed rebars to mend cast-in rebars
While building at the Nehru Palace metro station, some of the steel couplers became misplaced, and we were brought in to see what could be done.
ROME ITALY
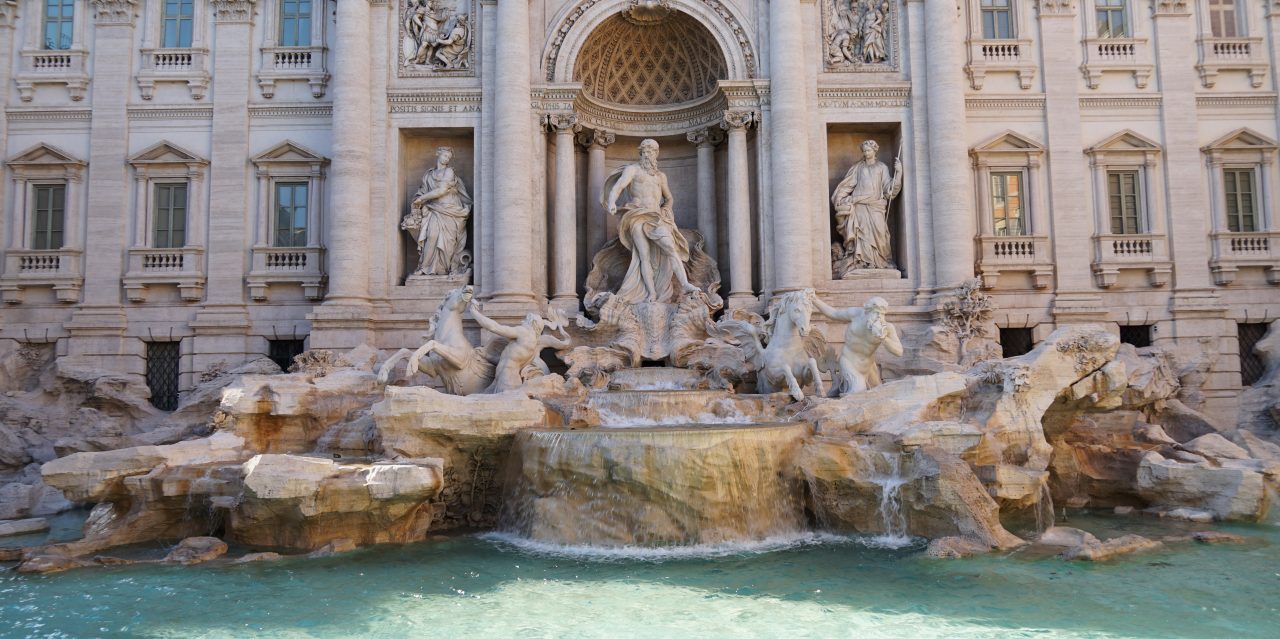
Post-installed rebar and anchoring technology
During the restoration of the Trevi Fountain in Rome, one of the columns in the façade was found to be unsafe, with a crack around its base.
HONG KONG
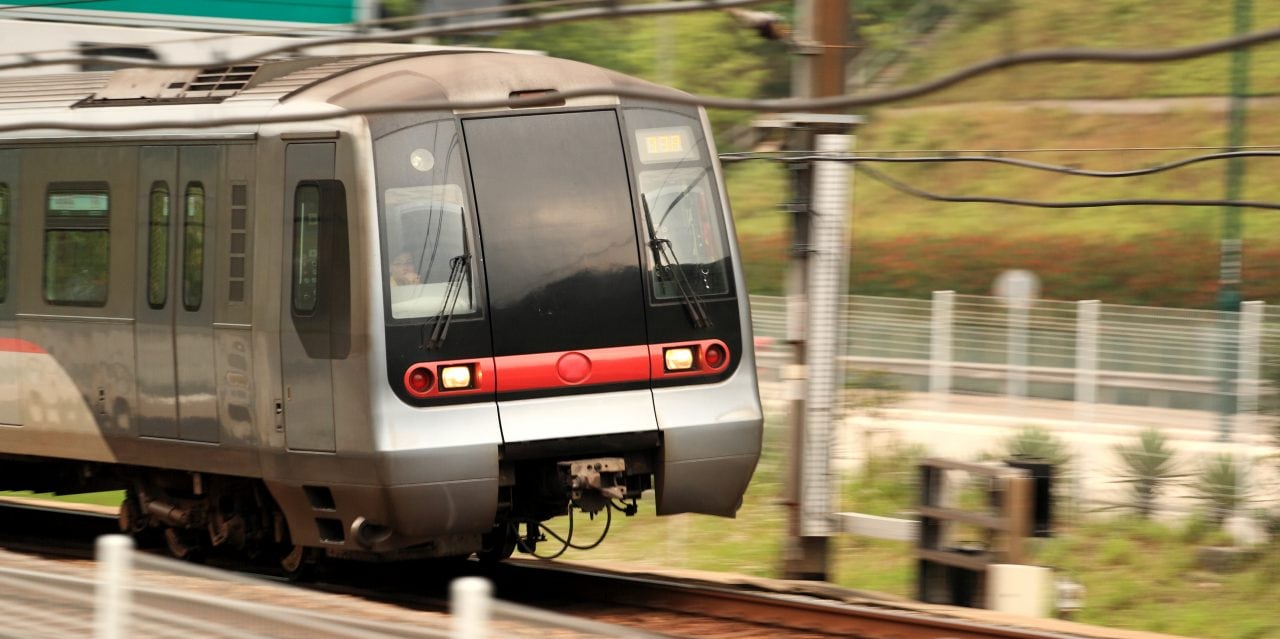
Post-installed rebar dust reduction with Hilti SafeSet™
When the MTR decided to build a new lift for one of its stations at the Lai King stop, it was crucial to keep dust to a minimum.